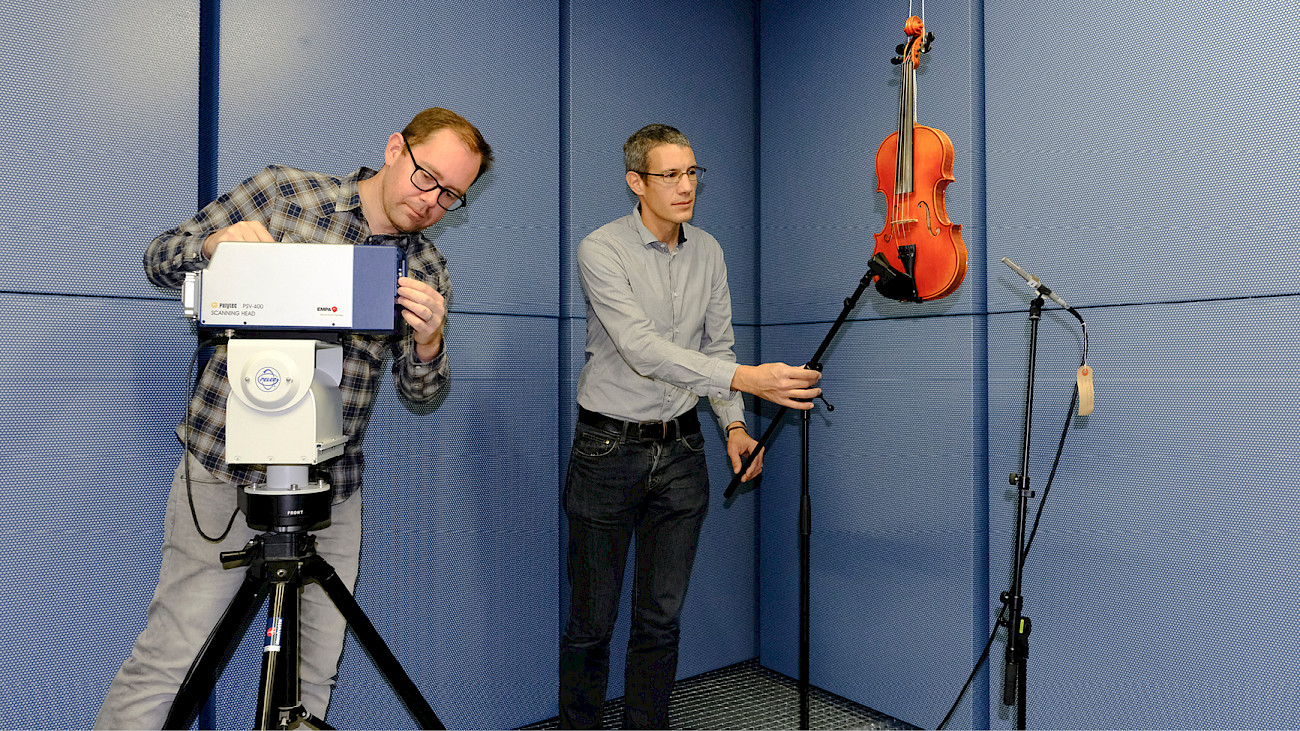
The Biotech Guarneri
In the laboratories of the Swiss Federal Laboratories for Materials Science and Technology Empa in St. Gallen and Dübendorf, wood researchers and acousticians have created biotech violins modelled on an 18th century master violin.
It sends a shiver down the spine at first: fungal infestation. But unlike on old, valuable written sources such as books, the findings on violin wood can be quite positive - especially if it was caused deliberately. It's a bit like a fine cheese: fungi can not only damage, but also enhance.
Wood refinement with mushrooms
A few years ago, wood researchers at the Swiss Federal Laboratories for Materials Science and Technology (Empa) were able to present a minor sensation: With the help of a fungus, they had succeeded in refining modern woods. Their properties were changed in such a way that under the microscope they were in no way inferior to the old woods of master violins such as a Stradivarius or a Guarneri.
"Today, trees grow faster and more unevenly than they did during a very specific cool period in the 17th century when the wood for Stradivari's instruments was growing," says Francis Schwarze from Empa's Cellulose & Wood Materials department. To modify modern spruce and maple woods, he used a fungus that causes so-called white rot in nature. "As soon as the wood structure had reached the desired state, the fungi were removed using a germicidal gas," says Schwarze. Experienced violin makers Michael Baumgartner and Paul Beley then used this fungus wood to make several sample violins. The model was the "Caspar Hauser" from 1724 - an instrument by the legendary master violin maker from Cremona, Giuseppe Guarneri, also known as Guarneri del Gesù. The scientific investigations entered a new round.
In the sound laboratory
At the Empa site in Dübendorf, the acousticians from the Acoustics/Noise Control department analysed the instruments in their sound laboratory. The conditions here are ideal:
The walls, ceiling and floor do not reflect the sound in a certain frequency band. Armin Zemp, who led the test series in 2018, explains the importance of such a room: "When we carry out tests in here, we have conditions as if we were in a free field. This means that everything we measure is not influenced by any reflections from the walls, which then reflect the sound back onto the object under investigation. We can actually rule out any influences from the surroundings. This room is therefore ideal for analysing the acoustic properties of the violins alone."
But it is not only an interference-free environment that is necessary for clean measurement results. The choice of instruments was also important to the researchers: In a series of measurements, they analysed a set of seven different violins. Six were made from the same tree and segment of untreated or mushroom-treated tonewood, as exact geometric copies of the "Caspar Hauser". There was also a genuine master violin from the 18th century. "There is also a modern non-master violin in the study series to have the upper and lower reference. This allows us to make statements about how relevant any differences between the treated and untreated violin are to be interpreted."
Artificial violinist and vibrometer
However, only the measurement results are analysed. To ensure that the interpretation skills of one or even several musicians are not assessed, a special violinist is used in the sound laboratory. Armin Zemp introduces it: "In this box we have an instrument that we call a shaker. You can use it to stimulate the string of the violin - where the bow actually passes over it. We can imitate a bow stroke without having to rely on a musician who constantly strokes a string for us over several hours. So this is our artificial violinist."
This electromechanical vibration exciter is connected to the measuring devices via the computer. It pits seven instruments against each other one after the other in a blind test. The acousticians do not know what kind of violin they are looking at.
In the so-called structure-borne sound measurement, the measurement data alone is to decide whether the violins made of mushroom wood can actually keep up with the sound of the old master violins. The acousticians try to identify differences in how the sound introduced into the instrument propagates and also whether the violins emit sound differently. To do this, the sound field emitted by the violin is measured using ten microphones. At the same time, the sound waves in the violin body are recorded using a scanning laser vibrometer. This device measures the frequency and amplitude of the vibrations at around 100 points on the violin body.
Acoustics researcher Bart Van Damme analyses the enormous amount of measurement results. He explains how any differences in the sound radiation of the old and modern violins come about: "The wood of the violins from the 18th century is a little heavier and stiffer. This is because it grew more slowly in the colder climate at that time. It is not just the stiffness alone that is important, nor is it just the density. It really is the combination of both. And according to measurements, this combination can be achieved with this fungal treatment. Mushroom-treated wood will vibrate at different frequencies than the same wood, structurally in the identical form, but which is not mushroom-treated. These differences in density and stiffness then also have an effect on the sound radiation."
These differences are visualised on the computer based on the measured values: images of violin bodies in rainbow colours are displayed, as seen on a thermal imaging camera. Various sound curves are also displayed.
From sound to sound
However, sound excitation is not yet what we perceive as sound, emphasises Bart Van Damme: "For us acousticians, it's first about a minimum amount of energy to make a convenient measurement - and not yet about sound. The decisive factor here is the relationship between string vibration, body vibration and sound, which is measured by the microphones. For Reto, the sound is really important, to get as close as possible to realistic tones. Does it sound like a violin should sound?"
Reto Pieren is a psychoacoustician at Empa. In a laboratory for hearing tests, he supervised further research, which followed the sound measurements of the violins in a next step: "In psychoacoustic tests, there are test subjects, i.e. people who listen to sounds and even music played on the test instruments. These people judge what they hear individually. In other words, they don't sit together and discuss it, but each person makes a separate judgement."
With the help of a computerised, randomised selection of questions, the psychoacousticians try to find out the sound characteristics of the individual violins and how they are perceived by people - as far as possible without personal interaction between the test subjects and researchers. There are different methods and questions for this: "Do you like instrument a better than b? Or: How do you like this instrument on a scale between 0 and 10? The aim is to achieve a consistent result at the end. Our listening tests tend to have between 20 and 100 test subjects. If two instruments are radically different, then you don't need very many test subjects to be able to measure differences. If the differences are smaller, you need more test subjects."
For the psychoacoustic tests to produce results that are as universally valid as possible, the group of test listeners needs a good mix, from amateurs to professionals. This includes sound engineers who spend their entire day dealing with the sound of instruments, or violins in particular. Daniel Dettwiler from Studio Idee und Klang brought them together as a group of experts for targeted listening tests and in-depth interviews. Human ears and high-precision measuring devices were used in equal measure on the way to the biotech violin made of mushroom wood, which is more than just an advertising gimmick. The result is not just a statement by euphoric hobbyists, but is based on profound findings from three areas: wood research, sound measurement and psychoacoustics.
The "Caspar Hauser II"
The time was ripe for the next step: after years of developing a new wood treatment process, after nine months in a mushroom solution, after production by two experienced violin makers and after acoustic and psychoacoustic tests in competition with other instruments and the public, the "Caspar Hauser II" was presented to the public. Our violinist Irina Pak was the first professional violinist to test the instrument. The project was made possible by Walter Fischli, whose main concern is that the violin is now being played: "The 'Caspar Hauser II' is our first mushroom violin, made from not yet optimal tonewood, and still a greenhorn. In the meantime, there are other Caspar Hauser series III and IV and mushroom wood violas. For all of them, playing in wooden instruments takes time. It remains to be seen whether it - together with other Mycowood violins - will continue to develop positively in the future." The idea of the patron, who himself holds a doctorate in biochemistry, would be to consistently promote young talent: "Ultimately, the aim is to create instruments that can be made available to talented young musicians with limited financial resources."
The foundation for this has been laid. Thanks to the interdisciplinary project, the acoustic properties of tonewood have been improved, i.e. they can be reproduced under standardised conditions. "This type of biotech wood modification could also avoid supply bottlenecks for valuable tonewoods," says wood researcher Francis Schwarze. The aim is to transform good raw material into exceptional tonewood and thus promote traditional musical instrument making in Europe. These are good prospects for the master violins of the 21st century.
We use deepL.com for our translations into English.